Author
David Fehrenbach
David is Managing Director of preML and writes about technology and business-related topics in computer vision and machine learning.
Time-of-Flight (ToF) sensors are a fascinating technology that has found applications in various fields when it comes to measuring tasks. In this blog post, we will explore the inner workings of ToF sensors and how they enable a wide range of applications.
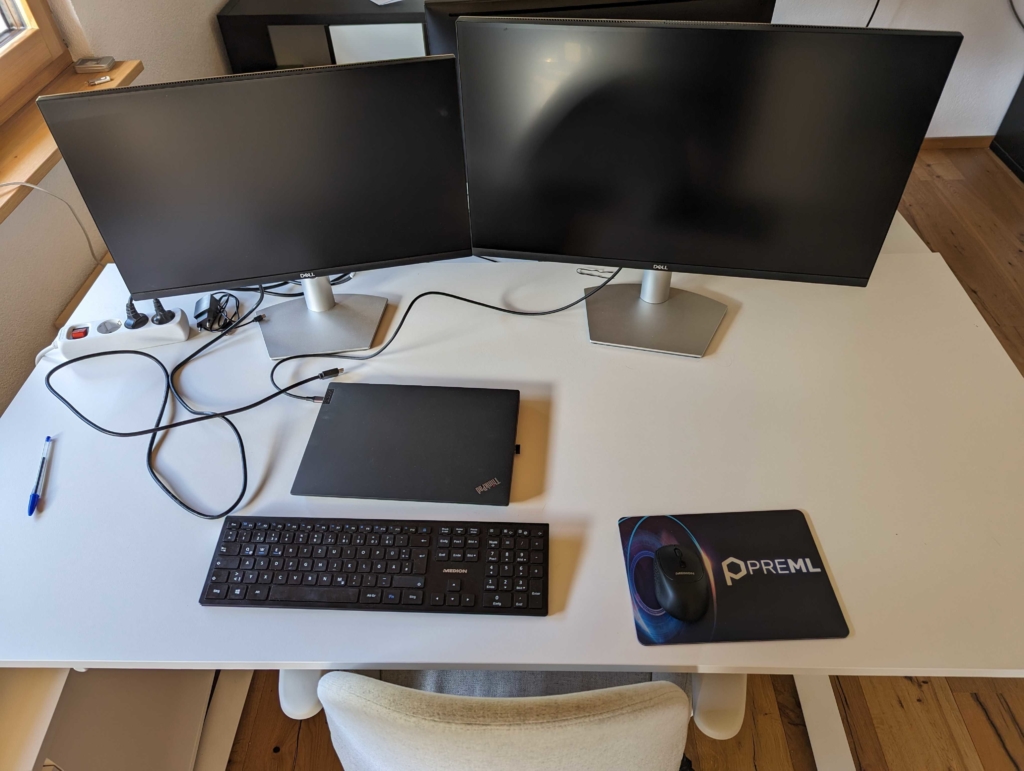
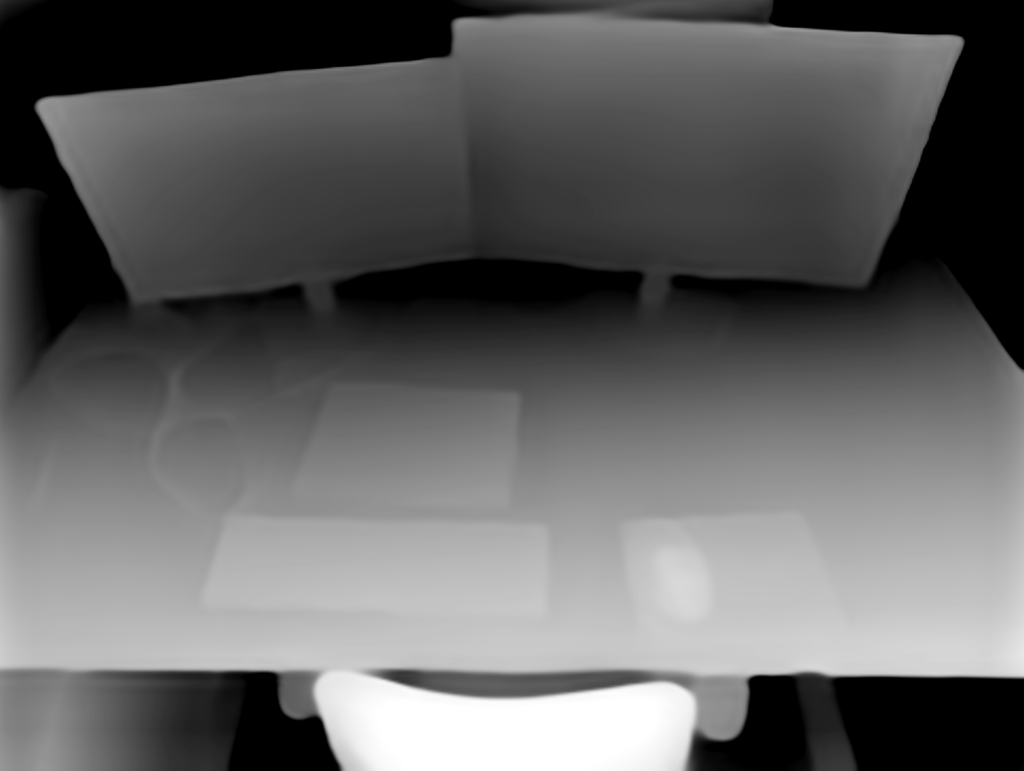
Image 1: Illustration of RGB camera output vs. TOF camera output.
Measuring Distance with ToF Sensors
A ToF sensor is designed to measure the time it takes for light to travel from the sensor to an object and back. This time measurement is then used to calculate the distance between the sensor and the object. Here’s how it works:
- Emitting Light Pulses: ToF sensors emit short bursts of infrared (850/940 nm) light pulses towards the target object.
- Light Reflection: When these pulses hit the object, they bounce back towards the sensor.
- Time Measurement: The sensor precisely measures the time it takes for the light pulses to travel to the object and back.
- Distance Calculation: Using the speed of light and the measured time, the sensor calculates the distance to the object.
This is done for a whole 2D array of pixels resulting in a depth map, i.e. an image which contains depth information instead of brightness information at each pixel.
Advantages and Challenges
ToF sensors are used in various applications in industrial automation. In the area of Machine Vision it is used for example to detect obstacles (e.g. in robotics), or to autofocus cameras. Further, it also works in classical quality control cases, such as for surface inspection when the geometry matters. Some advantages of ToF sensors are:
- Fast and Accurate: They provide real-time distance measurements with high accuracy.
- Low Light Performance: ToF sensors work well in low-light conditions.
- Non-Contact: They don’t require physical contact with objects, making them suitable for various applications.
- Images as Output: They produce images as output that can be processed using standard image algorithms, like those in our preML CVC Inspect Software.
However, typical challenges are that ToF sensors can be affected by ambient light, and they may struggle with highly reflective or transparent surfaces. Additionally, their accuracy can decrease over long distances.
In machine vision projects we always compare ToF with other 3D imaging technologies such as structured light, stereo imaging and laser profile scanning.
Exploring ToF Technology
In conclusion, Time-of-Flight sensors are remarkable devices and their ability to measure distance through the speed of light has unlocked exciting possibilities in automation.
If you’re considering the use of ToF sensors in your project or application, understanding their principles of operation is a crucial first step. Feel free to explore further or request a feasibility check to see how ToF sensors could benefit your specific needs.
Autor
David Fehrenbach
David is Managing Director of preML and writes about technology and business-related topics in computer vision and machine learning.